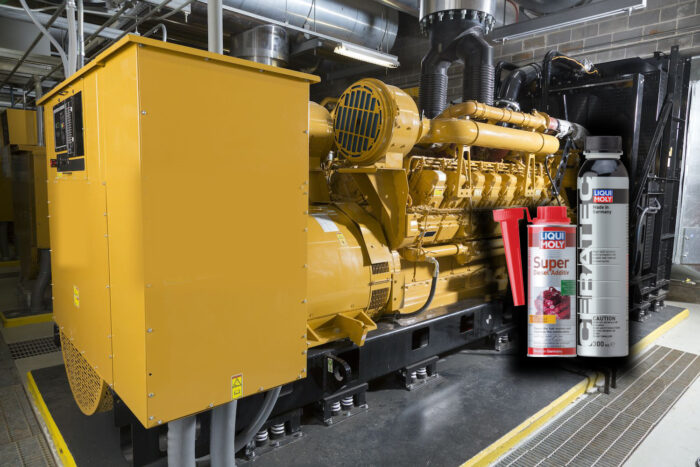
Contact me for more information: https://forms.gle/BWEGuryDvrGko5TJ8
BMG has teamed up with Liqui Moly – global leaders in additives, motor, transmissions and hydraulic oils – to offer cost saving solutions to the local generator market.
“As South Africa continues to face the exasperating challenges of daily load shedding and unplanned power outages, many companies are investing in alternative sources of power supply to maintain operations. Although emergency power generators are a popular choice to keep businesses running, the costs associated with running and maintaining these systems are often overlooked,” states Carlo Beukes, Business Development Manager, Agricultural, Automotive and Lubrication divisions, BMG. “Generators often operate at low efficiency rates, resulting in exorbitant diesel consumption and a significant erosion of company profitability.
“There are many reasons generators have a high oil consumption at times, including the use of incorrect or poor quality oil, which causes deposits to form on the piston and oil scraper rings that then seize. This means the crankcase chamber can no longer be sealed against the combustion chamber and as a result, fuel contaminates the oil that enters the combustion chamber where it is also burned.
“Liqui Moly lubricants and additives, which have been specially developed to reduce wear and extend maintenance intervals, ensure generators function perfectly and remain operational at all times. The additional use of additives makes fuels more stable and more ignitable, achieving greater efficiency, particularly with lower fuel quality. In addition, the use of additives reduces pollutant emissions and fuel consumption. Additives in the fuel can also improve the cetane number, clean the system and keep it clean. This means that less fuel is needed and there are fewer defective parts. As a result, there is less generator downtime. In addition, Liqui Moly additives protect the entire fuel system from corrosion.
“BMG and Liqui Moly specialists have joined forces to offer the local generator market a dependable solution that yields major savings in generator running costs. The costs of diesel and maintenance for generators can amount to up to five times more than the cost of Eskom electricity.
“As an example, an average-sized generator can consume up to 60 liters of diesel per hour. Considering that load shedding cycles sometimes last for up to four hours and occur three times a day, a single generator can easily consume 720 liters of diesel per day.
“Over the past three months, we have conducted accurate tests on-site at BMG World in Johannesburg. Results show a reduction in diesel consumption, ranging between 11% and 18% across the five generators used in the trial. When you consider the high daily volume of diesel consumed, these cost savings quickly accumulate. And by reducing diesel costs, a company’s earnings are boosted significantly.”
Liqui Moly’s Super Diesel Additive – which has been specially formulated for modern engines, fuels and demanding running conditions – contains a mixture of agents with cleaning, dispersing, material-protection and cetan-number increasing properties.
According to the BMG and Liqui Moly team, Super Diesel Additive has many benefits, including optimising engine performance, reducing fuel consumption and increasing the lubricating properties of the fuel.
Super Diesel Additive, which offers high wear resistance and corrosion protection, has also been formulated to boost the cetan number and to clean the entire injection system, by preventing the build-up of deposits and maintaining clean injection nozzles. A clean combustion is important because it protects the diesel particulate filter and prevents premature clogging.
Super Diesel Additive also improves cold-start properties, reduces injector failures, ensures smooth operation and reduces the risk of engine failures from oil dilution.
This is how Super Diesel Additive works: The injection pumps and injectors in state-of-the-art engines, with high system pressures and tight- fitting tolerances, are lubricated only by diesel fuel and sulphur-free or contaminated diesel fuels cannot always ensure the required lubrication.
The effective combination of lubrication improvers in Super Diesel Additive optimises lubricating characteristics of the fuel, protecting the sensitive components in the fuel system.
Due to greater ignition performance, the fuel shows improved combustion behaviour when the engine is cold and pollution from odours in the exhaust are significantly reduced.
Super Diesel Additive contains ingredients to increase the cetan number, facilitating combustion of the fuel and ensuring easy starting, smooth engine operation, better acceleration response and improved fuel economy. Low cetan numbers make it difficult to start the engine and reduce fuel economy.
During operation with standard fuels, deposits that form on the injectors have a negative effect on the function of the injector needle, leading to decreased fuel economy, oil dilution and increased contamination in the entire engine, as well as higher emissions. Regular use of Super Diesel Additive dissolves existing deposits and prevents new deposits from forming. Even small quantities of water and other aggressive contaminants in diesel fuel can damage metallic components in the fuel system. This additive forms a molecular protective coating on the metallic surfaces in the injection system, to effectively prevent corrosion damage.
These tests at BMG World also included the use of Liqui Moly Ceratec, where the recommended 6% ratio of Ceratec was added to the oil.
The immediate results were carefully documented and analysts observed significant benefits in engine performance – the most important of which was a notable decrease in the operating temperature, by approximately 7⁰C. In addition, the Scania generator alone exhibited a reduction in diesel consumption, resulting in a decrease from 52 litres per hour to 44.6 litres. This outstanding achievement translates to a fuel savings of nearly 16%.
Cera Tec is a micro-ceramic solid lubricant suspension based on hexagonal boron nitride (BN) in selected base oils, with exceptional resistance to high temperature and pressure. This product reduces friction and protects the engine and transmission against wear, thus extending service life of assemblies. Cera Tec also improves reliability of industrial equipment, lowers engine and transmission noise, minimises maintenance requirements and reduces downtime. Other benefits include energy savings, reduced risk of contamination, lower pollutant emissions and more efficient operating costs.
The graphite-like structure of resilient ceramic particles, with high mechanical and thermal stability, fill in the roughness in the metal of oil lubricated engines, transmissions, pumps and compressors, thereby preventing direct metal-on-metal contact. An active chemical utilises the existing friction energy to ensure a smooth-running effect that reduces fuel consumption in gasoline and diesel engines. The < 0.5 µm particle size guarantees optimum filter flow properties and protects against depositing of solid lubricant particles. Cera Tec is miscible with all industrial oils.
By including the results obtained from using Ceratec alongside Super Diesel Additive, a comprehensive and informative overview of the tests conducted has been provided. This additional information enhances the benefits and effectiveness of both products.
The BMG team works closely with key players in diverse sectors throughout Southern Africa to enhance production efficiencies, minimise downtime and extend the service life of critical systems at every plant.